Warehouse Racking System: Complete Guide to Types, Benefits & Choosing the Right Solution
- Warehouse Racking System
- Jul 11
- 4 min read
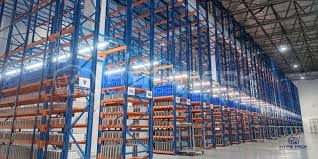
In the fast-paced world of logistics, space and efficiency are everything. Whether you're managing a small warehouse or a massive distribution center, a well-planned Warehouse Racking System can significantly improve productivity, organization, and cost-efficiency. This comprehensive guide will walk you through the various types of racking systems, how to select the right one, and why mezzanine storage can be a game-changer for your operations.
Understanding the Basics of Warehouse Racking
Warehouse racking systems are structures designed to store goods in a warehouse or storage facility. They provide a framework for efficient inventory storage and easy access to products, which enhances overall operational performance. These systems vary in complexity—from basic shelving units to multi-level pallet systems. Choosing the right type depends on several factors like storage volume, product type, warehouse size, and handling equipment.
Most systems revolve around pallet racking, which uses horizontal rows and multiple vertical levels to store palletized goods. When integrated correctly, racking systems improve inventory accuracy, minimize space waste, and increase throughput.
Types of Warehouse Racking Systems
Choosing the right racking system starts with understanding the various types available. Each serves a unique purpose based on warehouse needs, space, and inventory rotation.
Pallet Racking Systems
Pallet racking systems are the most common in warehouses. These systems store palletized goods in rows with multiple levels. They provide easy access for forklifts and are ideal for high-volume storage.
Selective Pallet Racking: This is the most basic and widely used system. It allows access to every pallet, making it suitable for businesses with varied SKUs. It offers flexibility and is easy to install and reconfigure.
Drive-In/Drive-Through Racking: Designed for high-density storage, this system allows forklifts to drive into the racking structure. Ideal for last-in, first-out (LIFO) or first-in, first-out (FIFO) inventory methods.
Push-Back Racking: Pallets are placed on nested carts that roll on inclined rails. When a pallet is loaded, it pushes the previous one back. This is excellent for maximizing space without sacrificing selectivity.
Pallet Flow Racking: Utilizes gravity rollers to move pallets from the loading end to the picking end. Great for FIFO inventory and high-throughput warehouses.
Cantilever Racking
Cantilever systems are ideal for storing long, bulky items like pipes, timber, or furniture. They use vertical columns with arms extending out, providing unobstructed access and flexibility in storage length.
Flexible Configuration: The arms can be adjusted to fit different product sizes, making this system highly adaptable to changing inventory.
Ease of Access: Forklifts can load and unload items quickly due to the open-front design.
Mobile Racking Systems
These high-density systems consist of racks mounted on mobile bases that move along rails. They allow you to eliminate multiple aisles, maximizing your storage capacity.
Increased Storage Density: Great for cold storage or expensive real estate where space optimization is critical.
Security Features: Often comes with lock mechanisms to restrict access, perfect for sensitive or high-value inventory.
Multi-Tier Racking Systems
Best suited for warehouses with high ceilings, these systems stack racking structures on top of each other, creating multiple access levels.
Maximized Vertical Space: You can multiply your storage without expanding your floor area.
Customizable Access: Walkways and staircases are added for safe worker access across tiers.
How to Choose the Right Pallet Racking System
The ideal racking system depends on your specific operational goals. Consider the following factors before making a decision:
Inventory Type and Turnover: Do you follow FIFO or LIFO? High-turnover items are better served with selective racking, while slow-moving items can be stored in drive-in racks.
Warehouse Layout: Measure the space accurately, considering aisle width, ceiling height, and entry/exit points.
Weight Capacity: Ensure the racking structure supports your heaviest pallets. Factor in safety margins and seismic activity if relevant.
Material Handling Equipment: Your forklift types and reach capabilities affect racking height and aisle width.
Budget vs. Long-Term ROI: While some systems are costlier upfront, they offer better ROI through optimized space and labor savings.
Benefits of Mezzanine Storage Systems
If you're running out of floor space but have vertical room to spare, a mezzanine storage system can double your storage area without relocating. These semi-permanent platforms are built between the floor and ceiling and can support racking, shelving, or even office space.
Cost-Efficiency: Expanding vertically is far more economical than relocating or building out.
Custom Design: Modular mezzanines can be tailored for any space and load requirements, with features like stairs, handrails, gates, and lighting.
Flexibility: These systems can be dismantled and relocated, offering adaptability to business growth.
Productivity Boost: Designated work zones or pick stations can be added on the mezzanine level to streamline operations.
Common Mistakes to Avoid in Warehouse Racking
Choosing the wrong system or poor implementation can lead to inefficiencies, damage, or safety hazards. Here are pitfalls to avoid:
Underestimating Load Capacity: Always calculate weight with safety buffers. Overloading is a major risk.
Neglecting Safety Features: Invest in rack protectors, aisle markers, and secure anchors to enhance warehouse safety.
Lack of Maintenance: Regular inspections ensure structural integrity and identify issues early.
Ignoring Workflow: A racking layout should complement your operational flow. Poor design slows down picking and increases labor.
Why Choose Hyperack for Your Warehouse Racking Needs?
Hyperack is Malaysia’s trusted expert in warehouse racking systems, offering tailored solutions for businesses of all sizes. Whether you need pallet racking, cantilever systems, mobile shelves, or mezzanine platforms, we deliver efficient, durable, and safe designs.
Local Expertise: We understand Malaysian industry needs and building codes inside out.
Customization: Our racking systems are designed specifically for your operations, not as one-size-fits-all.
Support & Installation: From design consultation to final setup, our team is with you at every step.
Conclusion
Investing in the right warehouse racking system can unlock your facility’s full potential. From maximizing space to boosting efficiency and safety, the right structure pays for itself over time. Whether you're choosing selective pallet racks, cantilever systems, or planning for mezzanine storage, take time to assess your needs—and always partner with an expert.
Ready to upgrade your warehouse? Explore customizable racking solutions at Hyperack Malaysia today.
Follow Us on Social Media
Stay updated with the latest trends and solutions for warehouse racking systems by following us on our social media channels:
📘 Facebook: https://www.facebook.com/hyperack/
▶️ YouTube: https://www.youtube.com/channel/UCdGZlojT4q3f0j9iIqv4OnQ
🎵 TikTok: https://www.tiktok.com/@hyperackofficial
📸 Instagram: https://www.instagram.com/hyperack/
📍 Google Map: https://maps.app.goo.gl/8BKAapohN7bsdZmf8
Comments